To meet the requirements of low-smoke halogen-free flame retardancy, a large amount of inorganic flame retardants must be added to wire and cable materials. During extrusion, the melt viscosity is large and the flow performance is poor, which is easy to generate frictional heat, resulting in excessively high local temperature of the melt. The material stays in the fuselage for a long time and is prone to decomposition. The gas produced by the decomposition is easy to form pores in the product. When extruding low-smoke halogen-free flame-retardant wire and cable materials, the following points should be paid attention to.
1. Before extrusion, the material should be dried to avoid pores on the cross section of the product.
2. Selection of processing technology. In addition to selecting a suitable extruder, the processing technology should also be reasonable. If the temperature is too high, the additive will decompose, resulting in pores in the product; if the temperature is too low, poor plasticization will occur. The fuselage pressure should be minimized as much as possible, and the screw speed should not be too high. Under the condition of ensuring that the material is fully plasticized, the extrusion temperature should be appropriately reduced. The processing technology should be adjusted according to different materials and different formulas.
3. Due to the poor fluidity of the material and the large friction resistance with the equipment, silicone can be added to improve the dispersibility of the inorganic flame retardant and reduce the processing torque. The addition of silicone can improve the flame retardant properties of wire and cable materials and is a good processing aid.
4. Selection of extruder. Since low-smoke halogen-free flame-retardant wire and cable materials have more additives and high melt viscosity, an extruder with a low screw compression ratio should be used. Ordinary single-screw extruders have low shear rates and poor mixing capabilities; twin-screw extruders have higher mixing capabilities, but processing highly filled low-smoke halogen-free flame-retardant wire and cable materials often causes material decomposition and discoloration due to excessive shearing. Therefore, a two-stage mixing extruder combining a single screw and a twin screw is selected. It is reported that a reciprocating single-screw mixer is currently the most ideal low-smoke halogen-free flame-retardant wire and cable material processing equipment.
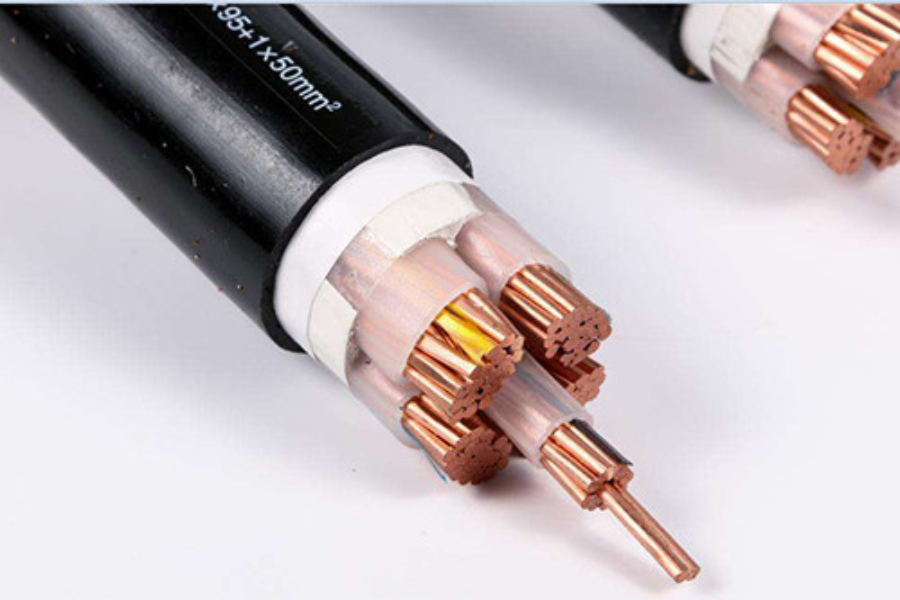
In short, low-smoke halogen-free flame-retardant wire and cable materials have strict requirements on processing equipment and process conditions. Appropriate extrusion equipment and process conditions must be selected based on raw material characteristics, product performance and extrusion characteristics.